Our Process
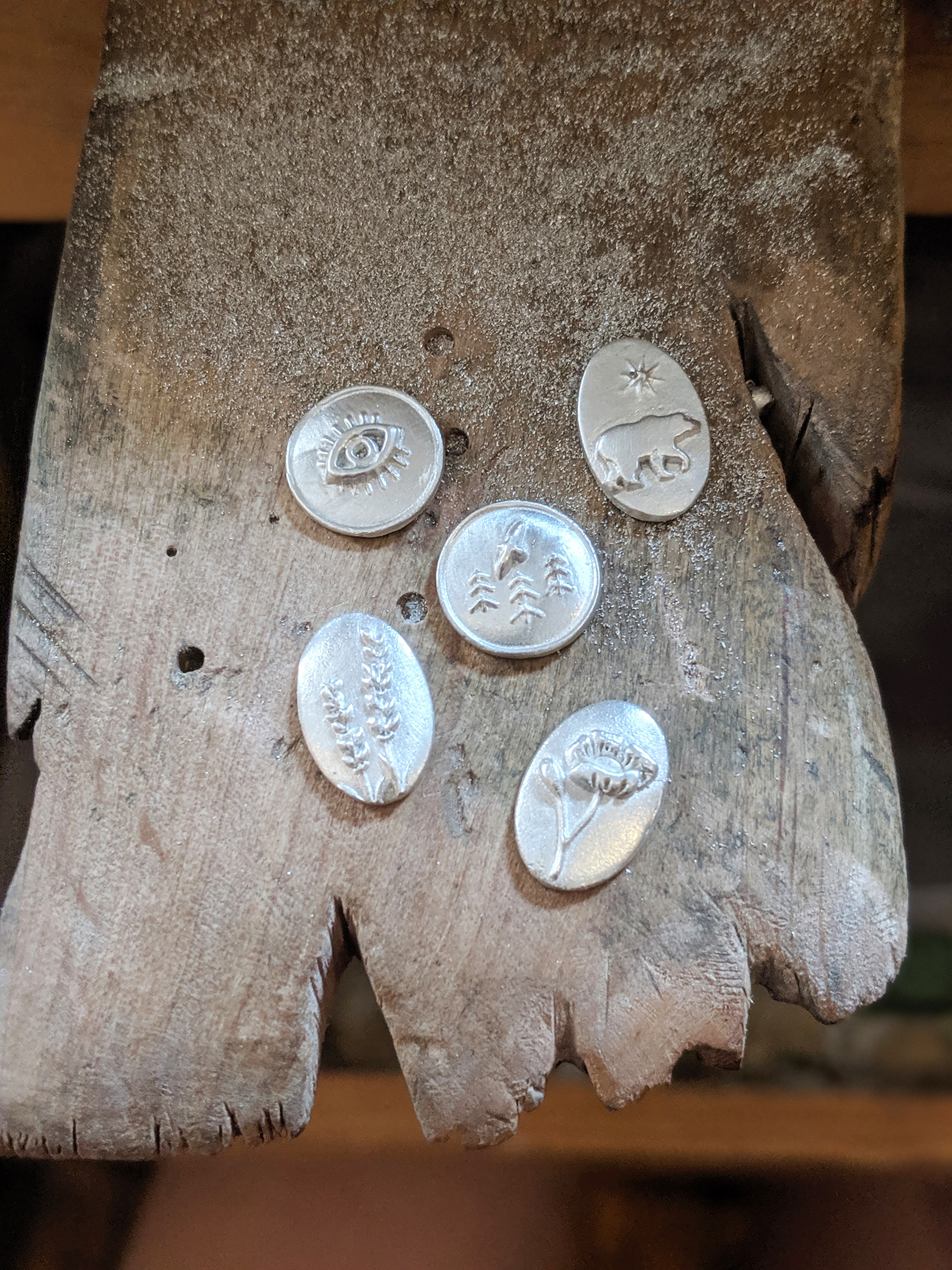
Each design begins with a master model. We use polymer clay or wax to craft our original models and then mold and cast them into metal.

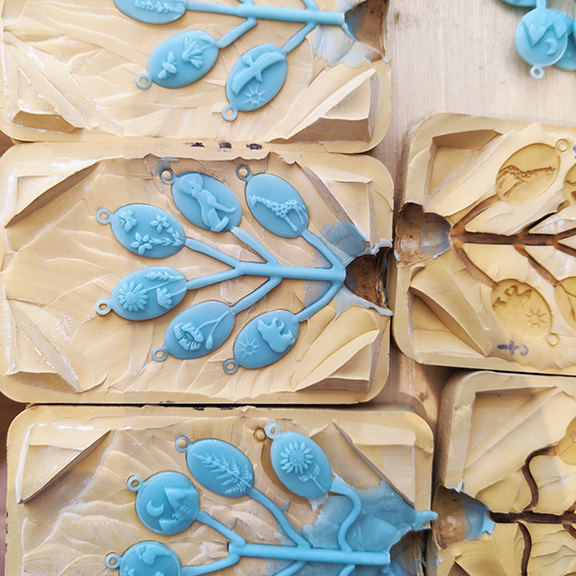
Rubber molds are made of the models, and then we use a wax injector to inject wax into the mold. The molten wax takes on the exact shape of the model. We have a lot of rubber molds! Each one is numbered and labelled so that we can locate each design quickly.
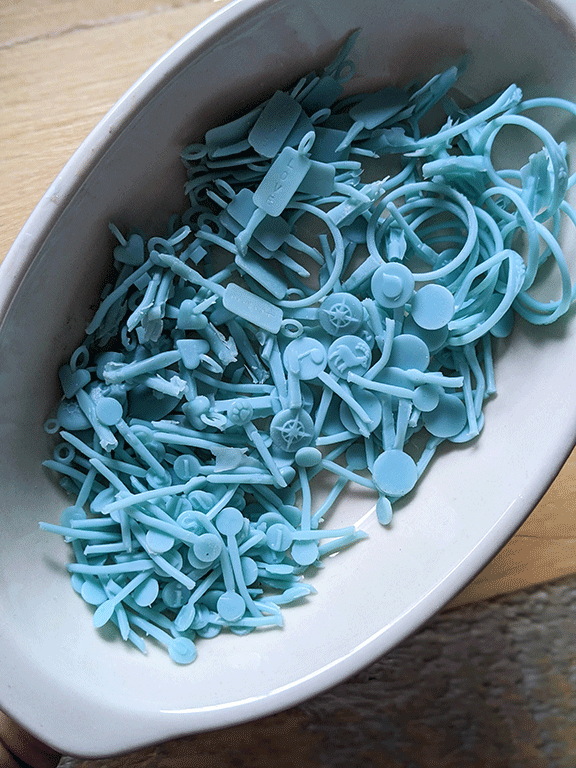
We pull a wax for every piece of jewellery that we make. Sometimes there are flaws or bubbles in the waxes, which can lead to flaws in the metal, as the final piece will take on the exact shape of the wax. Any misfits get thrown back into the wax pot to be reused.
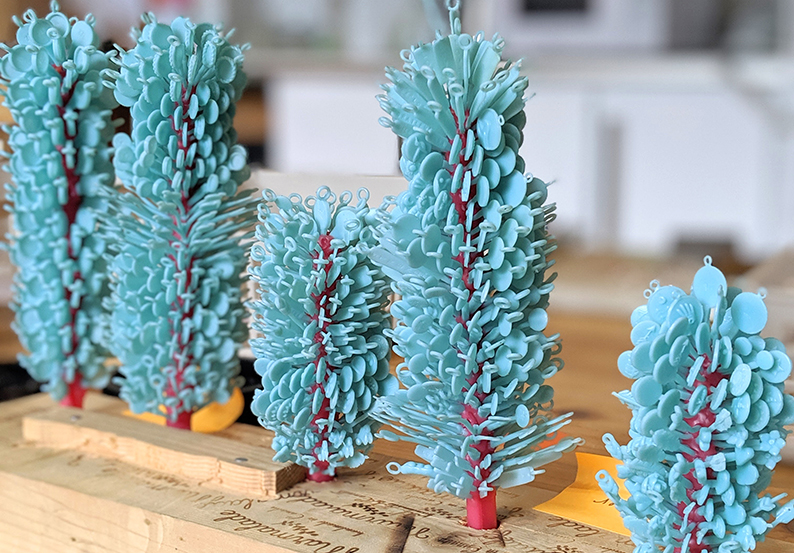
Using a wax pen, we attach each of the tiny waxes to a large sprue. Everyone in the studio enjoys this part of the making process. It's satisfying to squeeze as many pieces as possible onto one tree - while making sure that none touch each other.
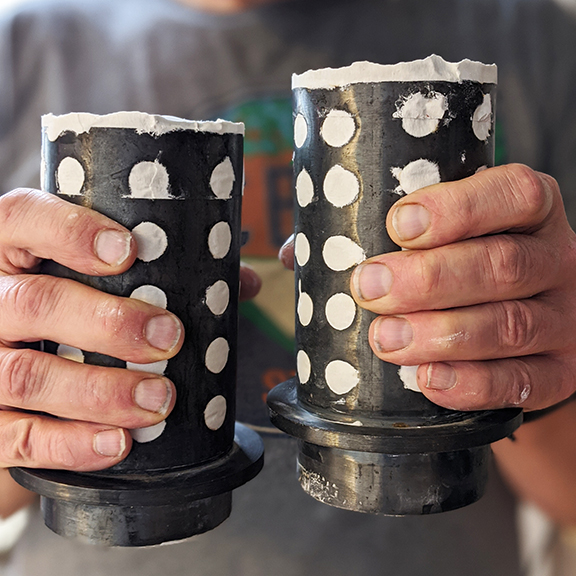
Dave mixes the investment, which is a lot like pancake batter. Except you have exactly 9 minutes to mix, vacuum out the bubbles, and pour before it hardens. He pours it into these metal flasks. The investment hardens around the wax trees, and then the flasks are put into the kiln for around 10 hours. The wax melts away completely leaving behind a cavity the shape of the wax
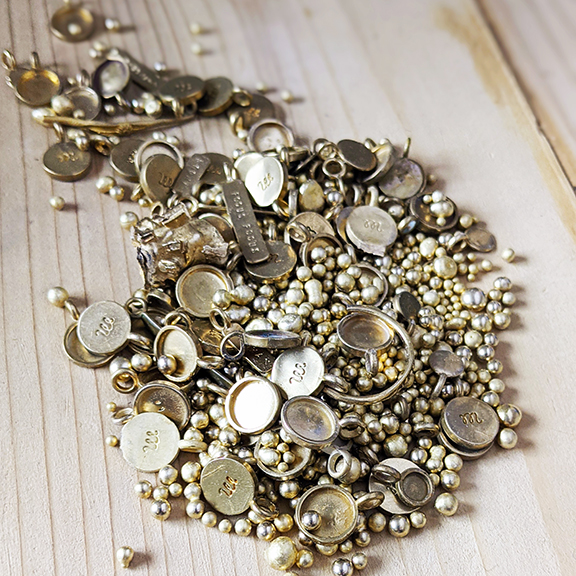
We mix sterling silver or bronze refined casting grain with our own metal that we recycle in the studio - pieces that didn't work out or didn't sell, and the centre sprues that are left over after each cast. Once that metal is made molten, Dave pours it into the flasks
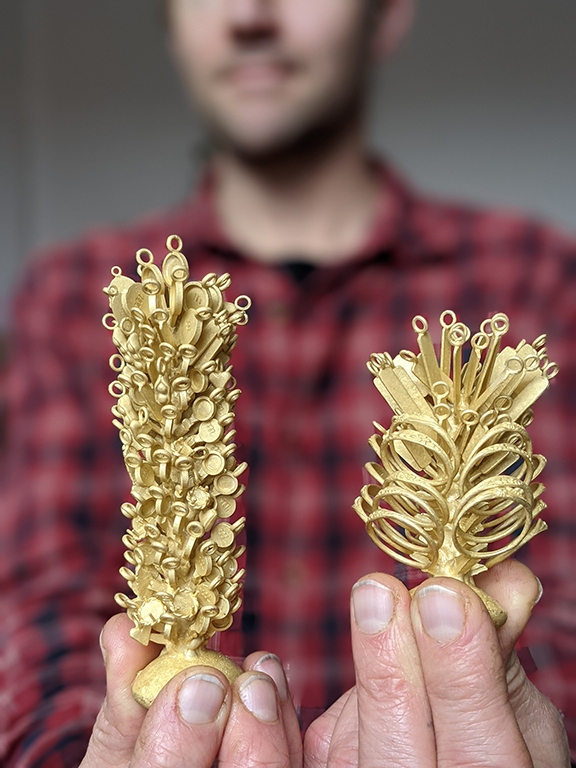
Washing away the investment reveals the metal beneath. Each charm or ring is clipped off of the tree. The bronze is a very hard metal, so this part requires a good deal of strength.
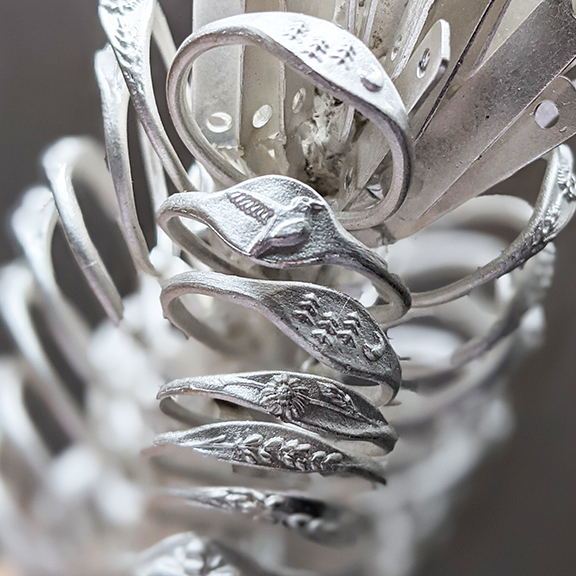
You can see that all of the details in the wax are translated into the silver. The metal is still very raw and rough at this point, but the shapes are there, and they are ready to be sized, soldered and polished.
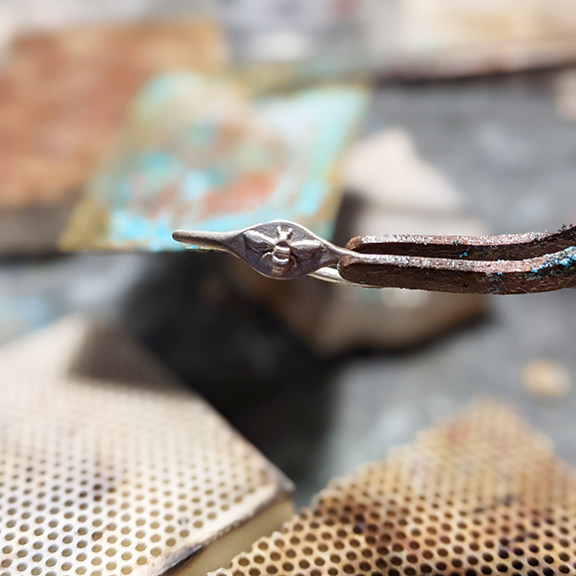
Our rings are cast in one size - size 8. So, we size each ring to order - adding metal for larger sizes and sawing out a portion of the band for smaller sizes.
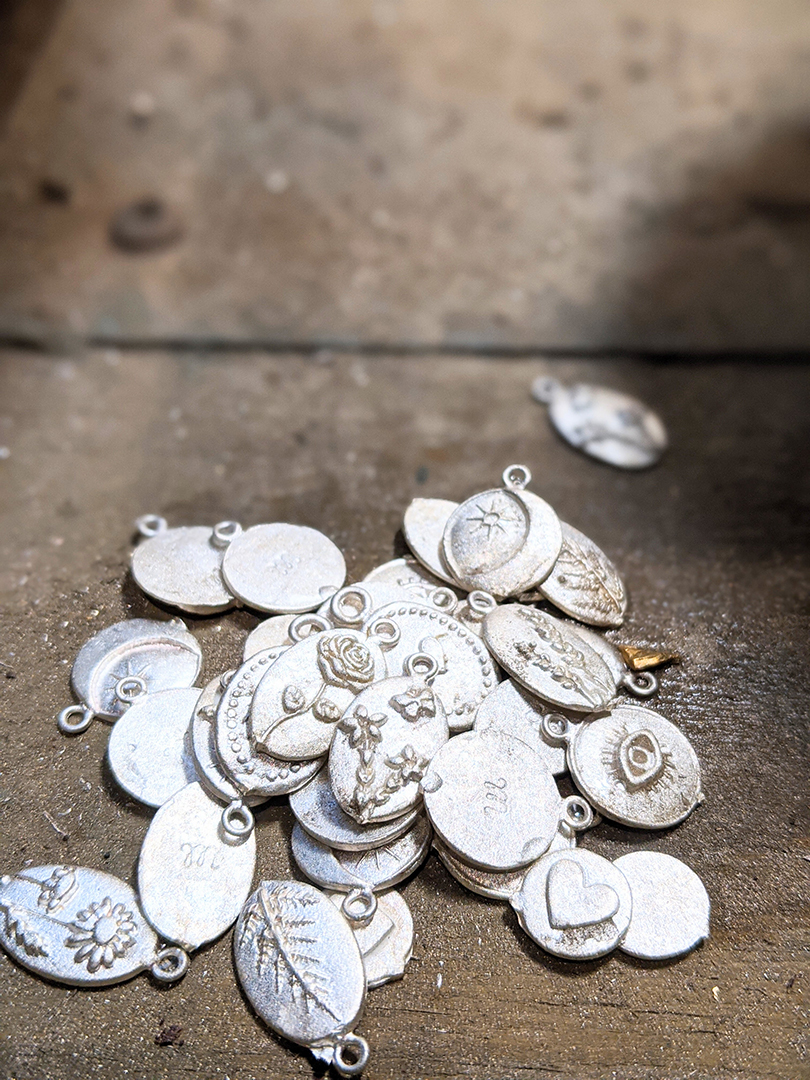
Once the charms are snipped from the tree, we grind off each sprue and file away any imperfections.
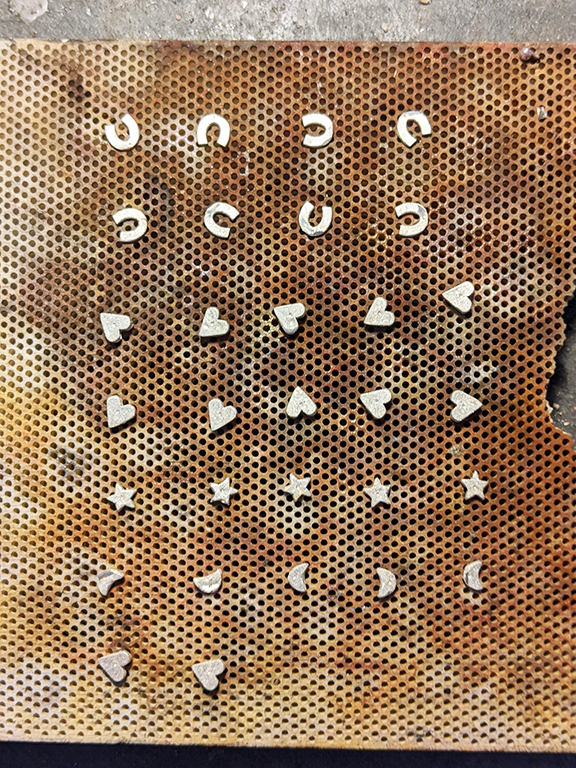
We solder sterling silver stud posts onto our sterling silver and bronze studs. They are nickel free and hypoallergenic.
.
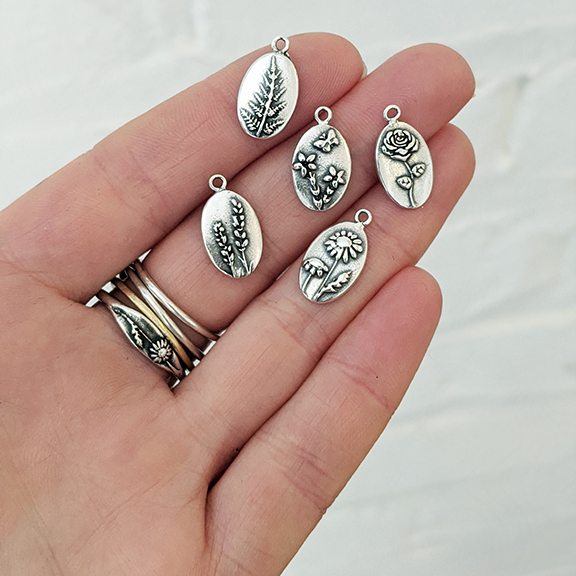
We apply a patina that highlights the recesses of each charm and then polish each one to a silky shine.
This process still feels magical to us in the studio. Creating something from nothing just doesn't get old. We hope that you've enjoyed learning about our process and that you can feel the hand of the maker in your marmalade creations.